The world of consumer electronics manufacturing is a race to make things smaller, thinner, more energy efficient and of course more cost effective. And to do all those, components will have to get smaller and smaller and more complex as integration continues to come into play.
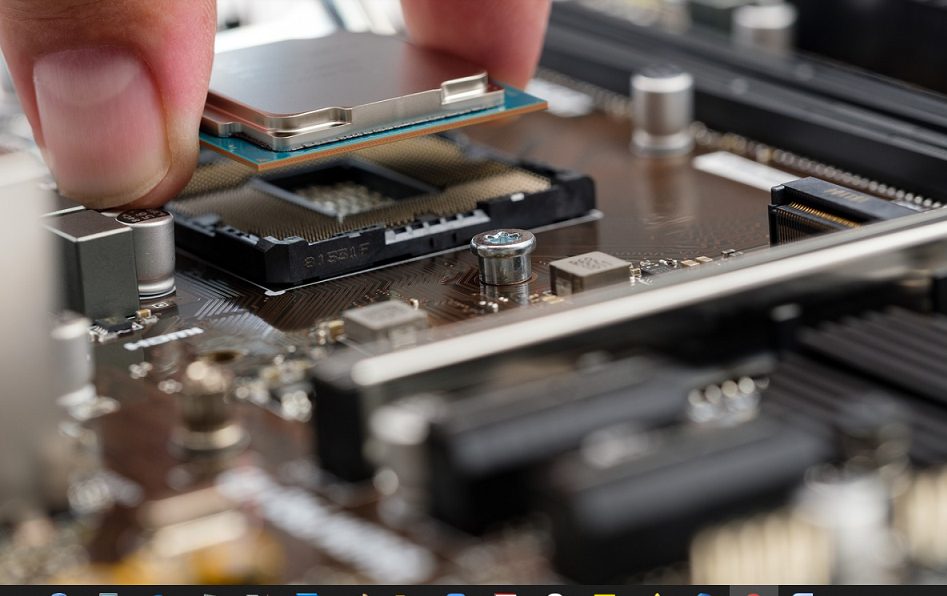
In the past, when it comes to consumer electronics manufacturing, the number of chips decides how much consumer electronics cost. Shortage or abundance of certain chips, the price of gold and copper, dictated supply and demand of many electronics products.
Many vintage computers were dependent on the supply of RAM chips. They were designed to operate with as few RAM as possible in order to be competitive. While some resorted to integrating many components to cut down on chip cost.
A Positive Effect
Cutting down on the number of chips is the reduced demand for electronics real-estate resulting in reduced PCBs. Also, for reduced amount of conductors used as well as the reduced materials for housings and casings, which in turn potentially reduces the footprint or thickness of the product.
Chip supply still affects consumer electronics manufacturing but not as much, thanks to the rapid pace of other technological innovations and more emphasis on aesthetics and functionality. For mobile phones, tablets and laptops, the thinner the better.
That means smaller parts and much more integration among components. Therefore, manufacturers are forced to make everything smaller. This is not just to become cost effective, but also to adjust to the aesthetic requirement demanded for today’s electronics. Smaller components such as transistors, resistors, capacitors and relays. There’s also the importance of reduced power consumption. The smaller the components are, the smaller the amount of power they can consume.
Components manufacturers are struggling and racing on how to make their products smaller and smaller to keep up with the demands of the top companies of consumer electronics manufacturing, such as Samsung, Huawei and Apple.
One way is by way of full integration. Through the creation of SOCs or Systems on Chips, a mobile phone is contained in just one chip.
Chips that used to handle audio and video are integrated with the processor. This cuts down on the chip count and raw materials as well as increases the processing speed and efficiency of the device. Components that cannot yet be integrated are left to other providers.
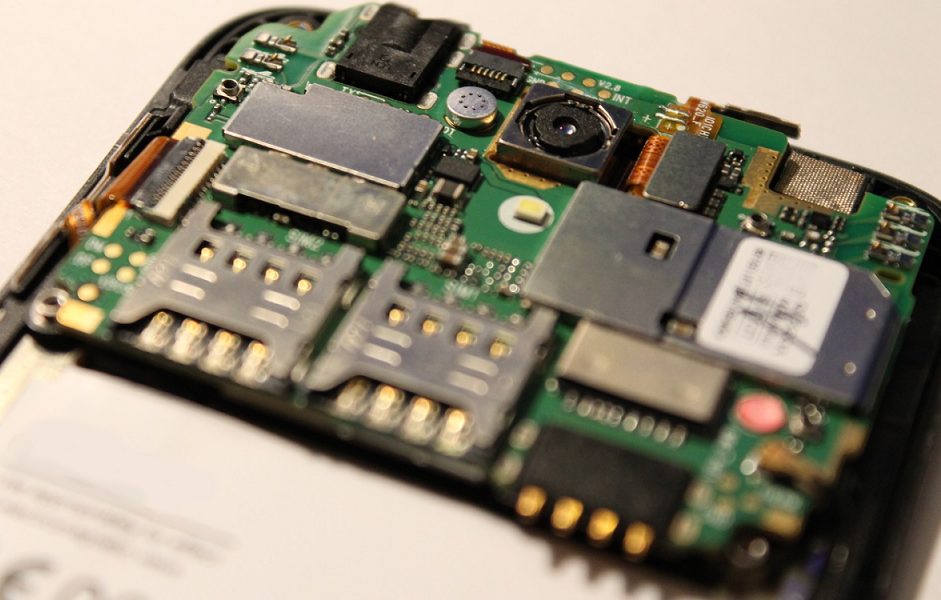
These manufacturers then scramble to license and acquire lower and lower nanometer technology for memory and processing units. They purchase new and update their fabrication equipment and production plants. Manufacturers are also keeping their eyes open for breakthroughs in nanotechnology and display technologies.
Examples of products that continue to get smaller in consumer electronics manufacturing include:
- Camera lenses and components
- Memory Modules and Micro-SD cards as they continue to increase capacity, maintaining their size yet increasing the number of transistors
- Microprocessors and graphics processors
- Thin film transistors in display screens continue to get smaller as screen resolutions become more densely packed.
It’s not only the insides that matter in consumer electronics manufacturing but the frames and housings as well. It’s easier now to tool smaller and more complex components through additive manufacturing or 3D printing. Components are made directly, or tooled from printed molds. They come in various shapes and sizes to support the internal components.
This is true for products such as Micro-SD cards, cameras and Bluetooth headsets. These smaller housings and frames are otherwise difficult if done through conventional tooling and molding. Along with new technologies, manufacturers also continue to research and come up with new materials for both the internal and external parts of consumer electronics.